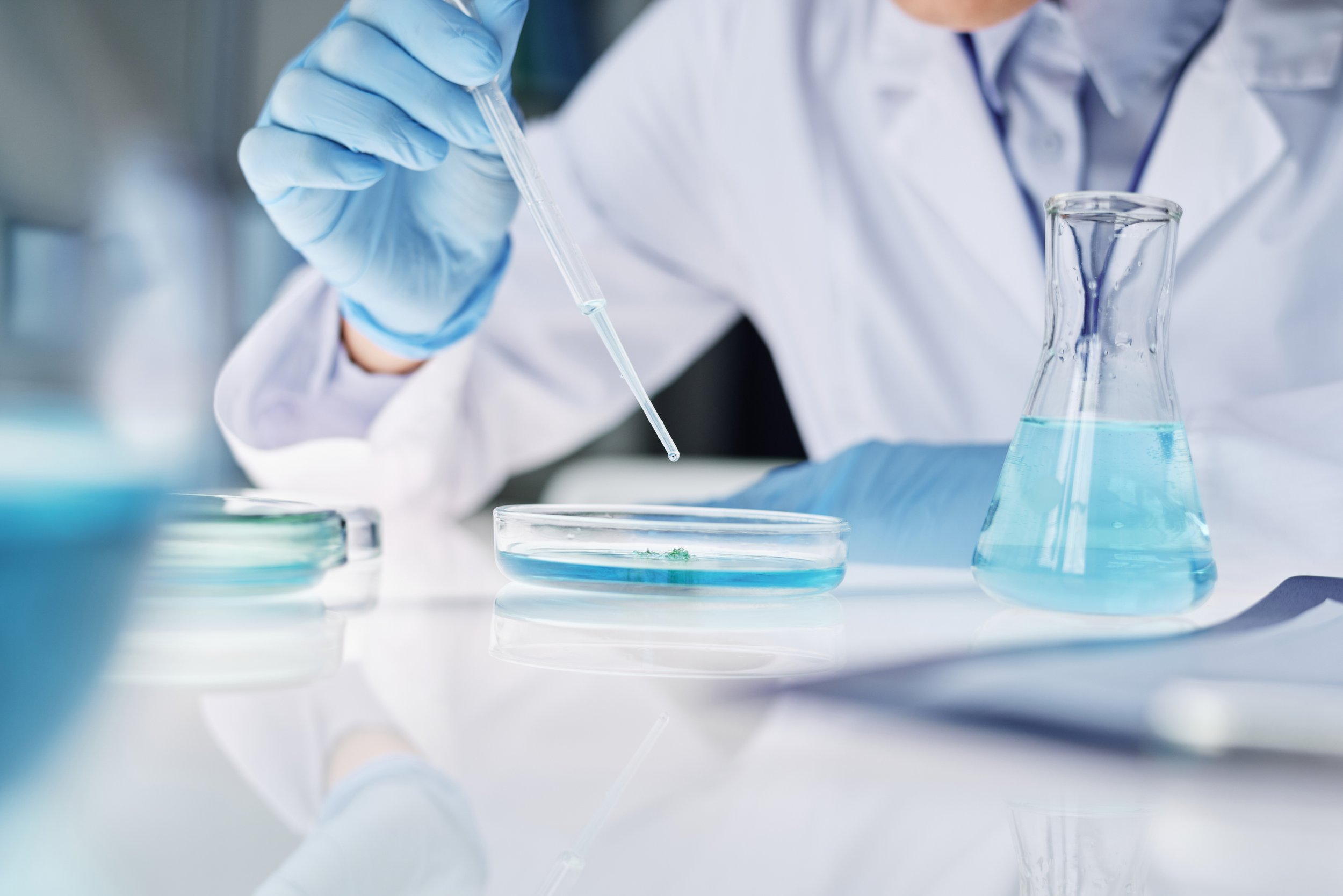
Life Sciences Consulting Collaborative.
LSc2 offers our clients in the pharmaceutical, biomedical & research sectors specialist front-end consultancy services in the design and delivery of controlled environment facilities for research and manufacturing.
We focus on technical advisory services for complex laboratory and cGMP cleanroom projects. These services include third-party peer reviews, feasibility studies, concept design & master planning, and the preparation of project briefs, project requirement specifications (PRS) and user requirement specifications (URS).
Our key clients include multinational and local manufacturers in the pharmaceutical and biomedical sectors, universities, research institutes and incubators, specialist health and pathology providers, industrial science parks as well as contractors, consultants & developers active in the Life Sciences.
Success through Collaboration.
About LSc2.
LSc2 was first founded in 2019 by Victor De Baets, a senior consultant and process architect with over 30 years’ experience in the planning, design, and management of projects in the research, pharmaceutical and biomedical sectors.
Victor brings specific specialist skills in the master planning, design & delivery of cGMP facilities for sterile parenterals (vaccines, plasma, mRNA, cell & gene therapy, and oncology), medical devices and solid/liquid dose manufacturing.
His approach reflects a solid understanding of pharmaceutical manufacturing processes and their cGMP implications. He is familiar with the regulatory requirements of TGA, FDA, EU and PIC/s, and has gained significant experience in the design of biomedical research containment laboratories to biosafety levels 1, 2, 3 & 4.
Intelligent Life Sciences Solutions..
Our Services.
Peer Reviews & Technical Advisory Services
-
Independent Peer Reviews and Specialist Technical Advisory Services assist our clients by derisking the design and delivery of complex controlled environment projects during the early stages of a project. These services may be delivered directly to the end-client, in partnership with other consultants or to building contractors.
We frequently partner with other consultants active in the Life Sciences, who rely on our specialist expertise for gateway reviews of their designs and documentation to ensure compliance with the applicable regulatory requirements. These may include Process Architecture reviews against the applicable cGMP’s (TGA/FDA/PIC/s) or layout reviews against the containment provisions of OGTR and DAFF – as an example.
Building Contractors tendering for and/or delivering complex cleanroom or laboratory projects, take advantage of our services to de-risk their tenders and ensure a successful project outcome. In the interest of time, more and more clients are tendering out projects with partially completed documentation that require early contractor involvement and design completion.
On complex cleanroom and laboratory projects this brings an element of risk for the contractor as critical details may not be fully resolved and/or missing from the documentation. In these heavily serviced and process driven projects, the devil (and cost) is in the detail. The client may also expect the contractor to take responsibility for managing design completion and the regulatory compliance aspects.
-
Our typical approach is to undertake a detailed review of the tender documentation from a cGMP and regulatory compliance perspective and identify what key information may be missing, if any. We raise potential opportunities for improving compliance and/or adding value to the project. We prepare a gap analysis of the missing information, categorizing this against their impacts on quality, budget, program and/or safety. We may also assist the contractor where required with tender strategies, submission writing, key differentiators and identification of other critical specialist inputs that may be required on these type of projects.
In some cases, the end-client instructs their lead consultant and/or contractor to engage our services on their project. In other cases, we are engaged directly by the client and provide our services on the client side and look after their interests as the project progresses from design & construction through to commissioning & validation. Typical services may include peer reviews of documentation at key gateways, participation in tender reviews and evaluation, participation in value engineering and constructability workshops, regular inspections during construction of the cleanrooms and/or laboratories and preparation of defects punch lists at practical completion.
-
Health Infrastructure NSW and Macquarie University: New mRNA Facility (Sydney, NSW)
Peer review of early concept design for NSW HI. (at Wood)
Tender support services to selected contractors. (as LSc2)
Health Infrastructure NSW: New Viral Vector Manufacturing Facility (VVMF) (Westmead Hospital, NSW)
Peer review of concept design including support with development of revised concept designs. (at Wood)
BioNTech: New mRNA Facility (Latrobe University, Melbourne, VIC)
Peer review of facility blueprint design (by others) against local regulatory and environmental requirements for BioNTech (at Wood)
Tender support services to selected contractors (as LSc2)
Feasibility Studies & Concept Designs
-
When considering a new project, the first step for our clients is typically the preparation of a business case to support application for funding, grants and/or internal approvals. Depending on the type and scale of the project, these business cases may be very detailed and include staffing and equipment costs, building design, construction and validation costs, operational costs, product unit cost drivers, etc.
At this early stage, there is typically no time or budget to bring a full design team on board to scope up a project and provide a detailed cost estimate of the facility – which is frequently the largest cost (and highest risk) of a project.
-
Our approach is to work closely with our clients to identify the potential facility requirements. This may involve a structured briefing workshop and the preparation of a high-level project scope document of Project Brief.
This information is used as the basis for preparing quick high level concept layouts – these would typically capture the critical major equipment items, and may also include cGMP zoning, process/personnel and waste flows, containment barriers and other critical information that impacts footprint and cost. These sketches may be hand drawn to scale but are typically sufficient for the preparation of a preliminary cost estimate by a Quantity Surveyor, or a Building Contractor experienced in this type of work.
This approach provides a level of rigor to the business case process and the confidence that the facility design and budget are in the required ballpark. This will avoid potential cost blowouts and other surprises down the track when it may be difficult to obtain additional funding or change the design/location of the building.
-
Confidential client: New mRNA Facility (Queensland)
Peer Review of business case concept design (at Wood)
Preparation of revised concept design and test fit of existing facility (at Wood)
CSL: Project Hawara Feasibility Study (Melbourne, Victoria)
Lead architect of a feasibility study for the relocation of CSL’s corporate headquarters from Parkville into a new 17-storey building in Melbourne’s CBD. This included the relocation of the clinical manufacturing cGMP facility (CMF), the recombinant product development group (rPD) and the R&D laboratories (at Billard Leece Partnership)
CSL Seqirus: Project Banksia Feasibility Study (Parkville, Victoria)
Lead architect of a feasibility study (for a new cell culture flu vaccine facility, anti-venom & anti-toxin (AVAT), Q-fever vaccine facility and new fill-finish facility, to be located at the Parkville site.
Masterplanning
-
A Site Master Plan (SMP) for a Pharmaceutical or Biological Production Facility provides a clear client vision for the site and sets the foundation and overall strategy for all development on the site, current and future.
The PharmaBio industry is a dynamic sector faced with ever changing forecasts, the rise of new modalities, increasing competition and unit cost reduction pressures, increasing environmental considerations, the ratcheting up of regulatory compliance requirements, strict quality, safety and security considerations, staff attraction and retention pressures, just to name a few. All these aspects need consideration when planning a new greenfield production site or considering modifications to existing sites.
The type of SMP’s range widely in their level of resolution and complexity and can range from a relatively simple high level architectural blocking and stacking diagram to a fully comprehensive SMP Study including production capacities, equipment requirements, utility load calculations & sizing, storage requirements and head counts for short/mid- and long-term scenarios.
A well considered SMP will have clearly defined functional adjacencies, clearly defined GMP zoning and unidirectional flows for personnel, materials, equipment & waste. It will consider future flexibility and expansion paths for all critical areas in the plant, it will define expansion strategies for black and clean utilities, waste management strategies (liquid, solid and gaseous waste), clearly defined site garmenting strategy and procedures.
Finally, it will consider the appropriate construction typologies for different parts of the facility based on local conditions, availability of materials and regulatory requirements.
LSc2 brings the skill sets to deliver architectural SMP’s inhouse. For a comprehensive SMP’s we typically partner with other consultants to bring the additional skills required such as process and services engineering, budgeting and programming and other specific specialists that the project may require.
-
We apply a structured three step approach:
Step 1 – Business Objectives & Existing Conditions Analysis
Data collection form each department
Data Review & Gap Analysis
Strategy
Step 2 – Develop Options, Evaluation and Selection
Site Strategy in context of Technical Implications
Development of Site Layout Options
Agree on Evaluation Criteria
Evaluate Options and Select Preferred Option
Step 3 - Delivery of the Completed Plan
Develop Preferred Option
Investment & Staging
-
Our experience in Site Master Planning has been gained over 30+ years of planning cGMP Production facilities for major local and international PharmaBio companies. We bring extensive experience in stakeholder management, data analysis and identification of potential design solutions and options.
BioNTech: Site Master Plan (TUAS Singapore)
Peer review and technical advisor on the site master plan and feasibility study for new mRNA, Cell & Gene Therapy and ADC production facility. The project consists of the repurposing of an existing solid-dose facility and includes fill, finish, inspection, and packaging (FFIP), GMP warehousing and freezers and new centralised utilities (LSc2 in collaboration with Wood).
Zoetis: Various studies for new Animal Vaccine Facility (Victoria and NSW)
Lead architect on various feasibility studies, site master plans and concept design for a new Greenfields animal vaccine production facility. The facility included ººstaff amenities & change facilities, administration and staff training, vaccine production, FFIP, QC & R&D laboratories, GMP warehousing, centralised utilities, and associated site infrastructure. (at Wood)
CSL Behring: Project Aurora, (Broadmeadows, Victoria)
Site master plan for a new Greenfields base plasma fractionation facility, including new centralized utilities, automated warehousing, -28ºC freezers and associated support areas. The project included a detailed review of the integration of the new central warehouse with the remainder of the operations on the site (at Billard Leece Partnership)
Project Briefing
-
The project brief is the foundation of any project and therefore vitally important. A solid, well-considered project brief will inform subsequent design phases and will be used as a design verification reference point for the life of the project.
LSc2 brings extensive Project Briefing experience on complex projects ranging from university research institutes to large pharmaceutical and biotech manufacturing facilities. The aim at this stage of the project is to drive a positive process of discovery with the user groups and ask the relevant questions in a collaborative environment that builds consensus and ownership of the project. As specialist cGMP Cleanroom and Laboratory designers we translate the needs of the manufacturing process and the research science into a building strategy. The aim is to accurately define these project needs, balanced against the project vision, program and budget.
-
We apply a structured methodology to the briefing process focused on interactive workshops with user groups that capture the functional intent and requirements of the project. User Groups are carefully managed to allow a high degree of intellectual exchange. A range of briefing tools are used to optimize the process including briefing questionnaires, functional area schedules, internal staff structures, adjacency diagrams, equipment lists, storage requirements, and functional descriptions. Depending on the type of project, this may also include individual Room Data Sheets.
User Group and Stakeholder management are a key focus of our activities. In larger organizations, the logistics of organizing regular workshops, ensuring the attendance of the relevant parties, coordinating their inputs and obtaining consensus is an intrinsic part of the briefing process. At the start of the project, user groups are formed, and a meeting plan prepared that would typically allow for:
Project Kick-Off Workshop & Site Visit
Visioning Workshop including benchmarking against other recent relevant projects
A series of pre-defined briefing workshops
Briefing Review Session – Present status update of briefing information and seek feedback
Draft Brief Review
Final Brief Presentation
At this stage it is important to focus on the bigger picture requirements - with sufficient detail to scope the project, but not too much detail that would bog down the briefing process. Once the project proceeds into Concept and Detailed Design, iterative workshops with the user groups would continue to allow the collection of additional layers of detail required for the design to develop.
-
Australian Red Cross Blood Service (ARCBS): Project Brief Preparation for Sydney and Melbourne Operation Centres (NSW & Victoria)
Project lead for the preparation of the functional project briefs for the new ARCBS Sydney and Melbourne operation centres. This included a strategic review process of their national operations with the ARCBS senior leadership team. (with S2F)
Charles Sturt University (CSU): New Veterinary Diagnostics Laboratory (Wagga Wagga, NSW)
Project lead for the user group management and preparation of the functional brief for a new PC3 veterinary diagnostics laboratory at the Charles Sturt University Wagga Wagga Campus. (with S2F)
Charles Sturt University (CSU): New Equine Isolation Facility (Wagga Wagga, NSW)
Project lead for the user group management and preparation of the return of brief for a new containment equine isolation facility. (with Billard Leece Partnership)
PRS & URS Preparation
-
Different terminologies are used in the construction industry to describe a Project Brief – these may include Return of Brief, Functional Brief, Project Plan, Client Project Requirements, Project Outline, etc. The Pharmaceutical Industry typically refers to Project Requirements Specification (PRS) and User Requirements Specification (URS).
The PRS typically outlines the detailed requirements for the overall project. It serves as a guide for all stakeholders to understand what needs to be accomplished and will cover the cGMP as well as the non-GMP areas of a facility.
-
The URS is a GMP Controlled Document focussed on the GMP critical aspects of a project. User Requirements Specifications address performance, functional (operation) and design (construction and installation) requirements. It defines the requirements of the product and the process that will form the basis for the validation. Identification of critical process steps and parameters are key activities for validation.
The purpose of the User Requirements Specification is to cover “what the project is, what it should do and how well it should do it from the Users perspective”.
User Requirement Specifications must be written in terms that are measurable and are verifiable during testing. There must be traceability between the URS and other specification documentation for the project. A URS is more frequently used to define equipment, systems and process requirements, but can also used to cover the cGMP-controlled manufacturing areas of a facility. It does not cover non-GMP critical areas such as staff and admin areas, black utilities, R&D laboratories, etc.
-
At LSc2, we use the same methodology for preparing a Project Brief to generate Project Requirement Specifications and User Requirement Specifications, but then with a greater focus on the process & equipment aspects, the regulatory and quality requirements and the integration of this document into the overall project validation activities.
Given the GMP criticality of these documents they will be strictly managed in accord with GMP Controlled Document requirements of traceability, change control, record keeping and the use of controlled/uncontrolled copies on the project.
-
Mayne Pharma: Mulgrave Site Redevelopment Project (Mulgrave, Victoria)
Project lead for the full A&E scope of design, documentation, construction and validation of the Building 9 implementation works. This included preparation and/or contribution to the full suite of project documents including project management plans, design management plans, GMP document system, project requirement specifications, user requirement specifications, technical specifications, etc. (with S2F)
CSL: Project Hawara (Melbourne, Victoria)
Peer Review of URS documents for the clinical protein suite (CPS), the recombinant innovation centre (RIC) and the central preparation area (CPA) (prepared by CSL).
Design Driven Compliance.
Our Experience.
Pharmaceutical and Biomedical
Solid and liquid dose manufacturing
Plasma fractionation
Vaccine manufacturing
Cytotoxins and Potents
Cell culture facilities
mRNA/sRNA research, pilot, and commercial manufacturing
Cell and Gene Therapy facilities
Radiopharmaceuticals
Sterile injectables
Blow-Fill-Seal
Primary and secondary packaging
Automated cGMP warehousing and cold storage facilities
Dispensaries and product sampling facilities
QA, QC and R&D laboratories
Laboratories
Containment facilities (Biosafety Level 1, 2, 3 and 4)
QC and QA laboratories
R&D and research incubator laboratories
Vivariums – small and large animals
Veterinary diagnostics laboratories
Chemistry, analytical, microbiology and instrument laboratories
Nanotechnology research facilities
Intelligent materials research and pilot facilities
Pathology & plasma processing
Bioterrorism research facilities
Food, soil, and water testing
Plant and insect research
Teaching laboratories
We work with you.
Our Clients.
Our key clients include multinational and local manufacturers in the pharmaceutical and biomedical sectors, universities, research institutes and incubators, specialist health and pathology providers, industrial science parks as well as contractors, consultants & developers active in the Life Sciences.
Process Driven Design.
The Collaborative.
The LSc2 Collaborative is an informal professional network that provides our clients access to a talented group of respected and and experienced specialist consultants, contractors and suppliers offering services across process architecture, laboratory planning, services engineering, process & clean utilities engineering, cost estimating, programming, design/project & construction management, commissioning, and validation. Selected members of the Collaborative have successfully worked together and delivered major projects for our clients for some thirty years.
We work with you.
Get in touch with us by using this form.
Download our Capability Statement.
Enter your email address to download a copy of our Capability Statement.